In the realm of industrial automation, actuators play a pivotal role in converting various forms of energy into mechanical motion. Actuators are used extensively in a wide range of applications, from robotics and manufacturing to aerospace and automotive systems. Among the different types of actuators available, hydraulic actuators, pneumatic actuators, and electric linear actuators are commonly employed, each with its own set of advantages and limitations. In this blog post, we will delve into a detailed comparison of these three actuator types, examining their operating principles, characteristics, applications, and performance factors.
Hydraulic Actuators
Hydraulic actuators are devices that convert fluid pressure into mechanical force and motion. They utilize a hydraulic fluid, typically oil, to transmit force and perform work. Hydraulic actuators are widely known for their high power density, precise control, and ability to generate substantial forces. They are often utilized in heavy-duty applications where high force and torque outputs are required, such as construction machinery, industrial presses, and heavy equipment,
1) Operating Principle
Hydraulic actuators rely on Pascal’s law, which states that pressure exerted on a fluid in a confined space is transmitted equally in all directions. They consist of a piston, cylinder, and a hydraulic pump or motor. When hydraulic fluid is supplied to the cylinder, it pushes against the piston, generating linear motion.
2) Characteristics
Hydraulic actuators offer high force capabilities, enabling them to handle heavy loads. They also provide precise control over speed and position due to their inherent characteristics. Additionally, hydraulic systems can store energy, allowing for quick and powerful movements.
3) Applications
Hydraulic actuators find extensive applications in industries requiring high force and precise control, such as construction, manufacturing, and transportation. They are particularly well-suited for heavy machinery, earth-moving equipment, and hydraulic presses.
4) Performance Factors
Key performance factors for hydraulic actuators include power density, response time, efficiency, and maintenance requirements. Hydraulic systems require proper fluid filtration, regular maintenance, and skilled technicians for optimal performance.
Pneumatic Actuators
Pneumatic actuators, also known as air actuators, utilize compressed air to create mechanical motion. They are widely used in various industrial and automation systems due to their simplicity, quick response time, and suitability for applications where moderate force is required.
1) Operating Principle
Pneumatic actuators operate on the principle of converting compressed air energy into linear or rotary motion. They consist of a piston, cylinder, and a pneumatic control valve. Compressed air enters the cylinder, exerting pressure on the piston and generating the desired motion.
2) Characteristics
Pneumatic actuators offer quick response times and high-speed operation, making them suitable for applications that require rapid movements. They are also relatively compact, lightweight, and cost-effective compared to hydraulic or electric actuators.
3) Applications
Pneumatic actuators find widespread use in industries such as packaging, assembly lines, and pneumatic tools. They are commonly employed in tasks such as gripping, clamping, and linear or rotary motion control.
4) Performance Factors
Performance factors for pneumatic actuators include response time, force output, energy efficiency, and noise levels. Pneumatic systems may produce noise during operation, and their force capabilities are generally lower compared to hydraulic or electric actuators.
Electric Linear Actuators
Electric linear actuators utilize electrical energy to produce linear motion. They are widely adopted due to their precise control, versatility, and ease of integration into automated systems.
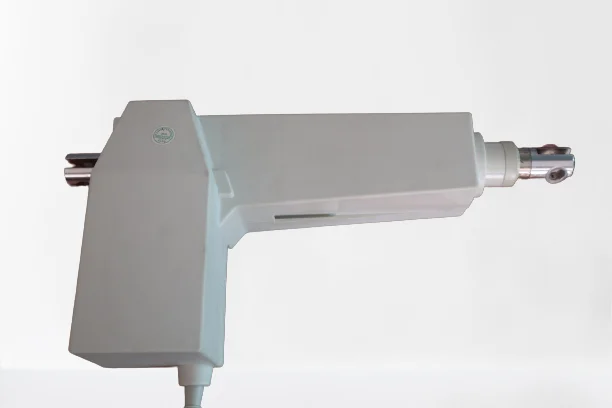
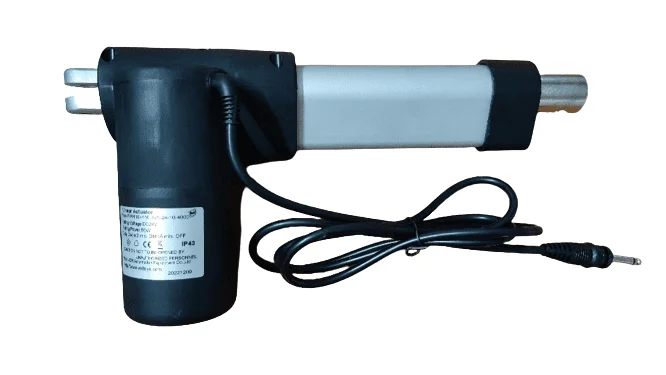
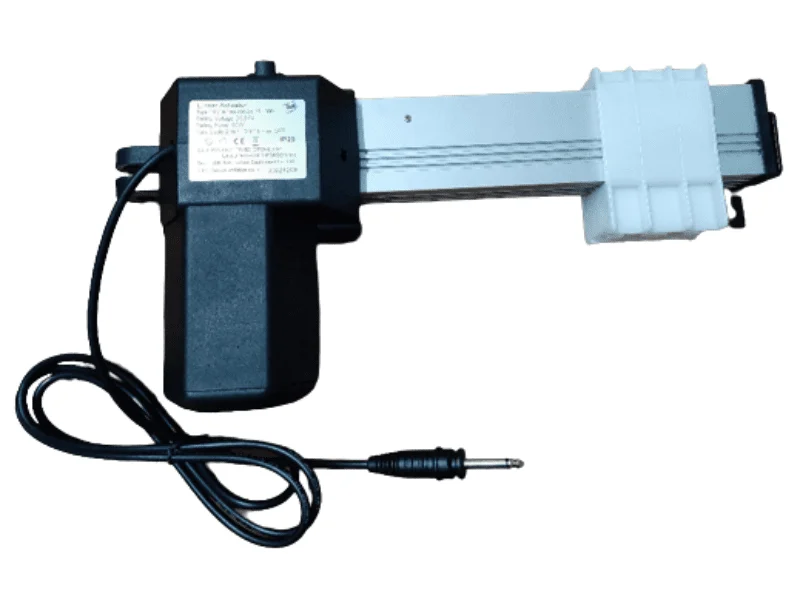
1) Operating Principle of electric linear actuators
Electric linear actuators employ an electric motor, which is typically connected to a screw or belt mechanism. When the motor rotates, the linear motion is achieved by the translation of the screw or belt.
2) Characteristics of electric linear actuators
Electric linear actuators offer precise control over position, speed, and acceleration, making them ideal for applications that require high accuracy. They are self-contained units, eliminating the need for external fluid or gas sources. Electric actuators are also known for their quiet operation and ease of installation.
3) Applications of electric linear actuators
Electric linear actuators find applications in various industries, including robotics, medical devices, and home automation. They are commonly used in tasks such as opening and closing doors, adjusting furniture, and precise positioning of components.
4) Performance Factors of electric linear actuators
Performance factors for electric linear actuators include speed, accuracy, force output, power consumption, and maintenance requirements. Electric actuators are highly efficient and offer excellent controllability, but they may have limitations in terms of maximum force output compared to hydraulic actuators.
Comparison and Summary of Electric Linear Actuators
1) Power and Force Output:
Hydraulic actuators provide the highest power density and force output capabilities among the three types, making them suitable for heavy-duty applications. Pneumatic actuators offer moderate force outputs, while electric linear actuators have more limited force capacities.
2) Control and Precision:
Electric linear actuators offer precise control over position, speed, and acceleration, making them ideal for applications that require high accuracy. Hydraulic actuators also provide precise control, but they may require additional control systems for fine-tuning. Pneumatic actuators offer less precise control compared to the other two types.
3) Speed and Response Time:
Pneumatic actuators have the fastest response time due to the instant availability of compressed air. Electric linear actuators can achieve high speeds, while hydraulic actuators tend to have slower response times.
4) Maintenance and Efficiency:
Electric linear actuators require minimal maintenance, while hydraulic actuators need regular fluid checks and filtration. Pneumatic actuators are relatively low maintenance as well. In terms of efficiency, electric actuators are typically more efficient than hydraulic or pneumatic ones.
5) Cost and Integration:
Pneumatic actuators are generally the most cost-effective option, followed by electric linear actuators. Hydraulic actuators are typically the most expensive due to the complexity of hydraulic systems. Electric linear actuators are often preferred for their ease of integration into automated systems.
Conclusion: Electric Linear Actuators
In conclusion, the choice between hydraulic actuators, pneumatic actuators, and electric linear actuators depends on the specific requirements of the application. Hydraulic actuators excel in high-force applications that demand precise control. Pneumatic actuators are suitable for tasks that require quick response times and moderate forces. Electric linear actuators offer precise control, high accuracy, and ease of integration into automated systems. By understanding the operating principles, characteristics, applications, and performance factors of each actuator type, engineers and system designers can make informed decisions when selecting the most appropriate actuator for their specific needs. For selecting actuators for specific applications kindly select the actuators from our Actuator Selection Table.