A few years ago, Rajesh Kumar, a plant manager at an automotive parts manufacturing unit in Chennai, faced a recurring problem. His factory relied heavily on pneumatic cylinders for automation, but frequent air leaks, inconsistent performance, and high maintenance costs were slowing down production. Every month, he had to halt operations for maintenance, leading to losses in both time and revenue, electric cylinder.
One day, while attending an industry seminar on automation, he learned about electric cylinder actuators. Skeptical but intrigued, he decided to test them in a small section of his production line. The results were astonishing—efficiency improved, energy consumption dropped, and maintenance issues almost disappeared. Seeing the success, he gradually replaced all pneumatic cylinders with electric actuators, revolutionizing his factory’s workflow.
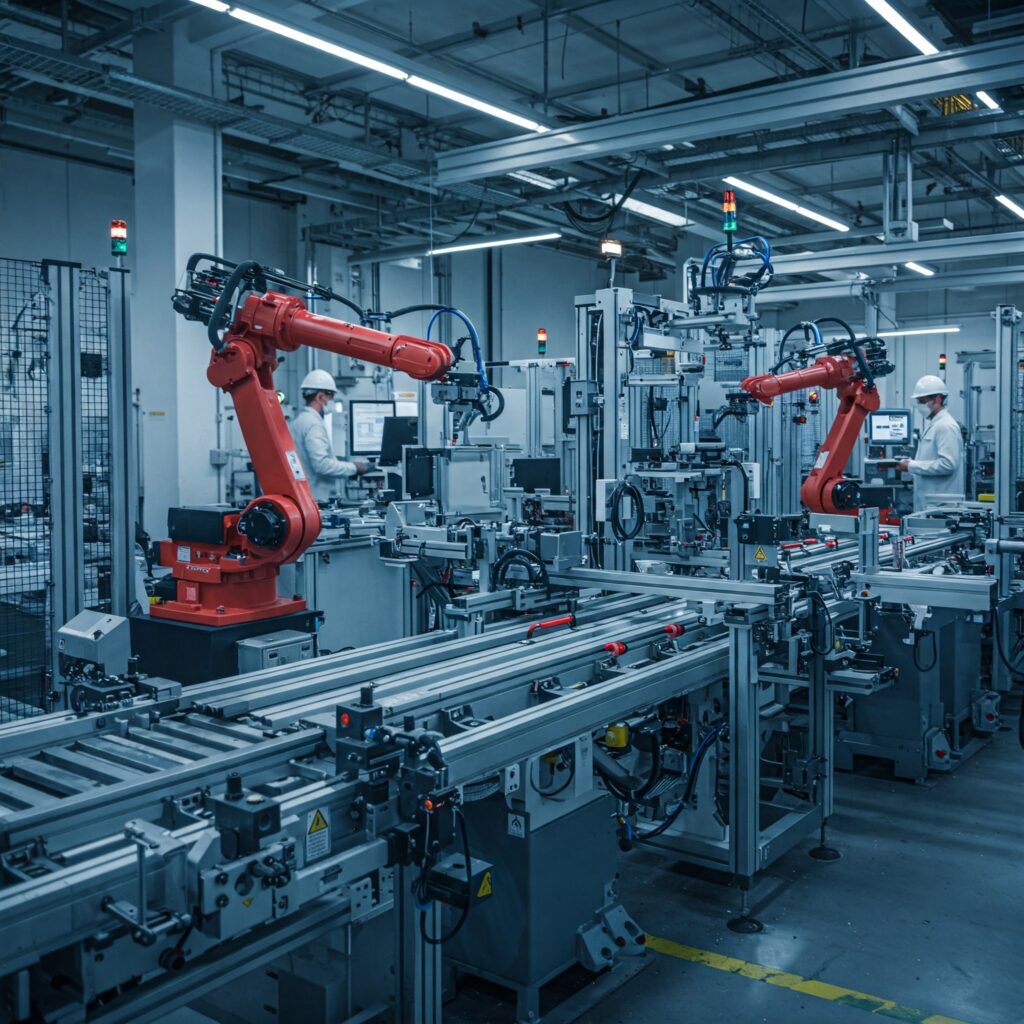
What Makes Electric Cylinder Actuators Different?
Electric cylinder actuators are linear motion devices powered by electricity instead of compressed air or hydraulic fluid. They use a servo or stepper motor connected to a lead screw or ball screw, enabling precise and repeatable movement. Unlike traditional systems, they do not require air compressors or hydraulic pumps, making them cleaner and more energy-efficient.
Why Are Indian Industries Switching to Electric Actuators?
The success of Rajesh’s factory is not an isolated case. Across India, manufacturers are shifting towards electric cylinder actuators for several reasons:
- Energy Savings: Unlike pneumatic cylinders that require continuous air pressure, electric actuators consume power only during movement, significantly reducing electricity bills.
- Superior Precision: With controlled motion and feedback mechanisms, electric actuators provide better accuracy and consistency.
- Minimal Maintenance: With no fluid leaks, clogged valves, or pressure fluctuations, electric actuators reduce downtime and increase productivity.
- Environmentally Friendly: Many industries are moving towards sustainability, and eliminating oil and air-based systems aligns with their green initiatives.
Real-World Applications in India
The use of electric actuators is rapidly growing in various Indian industries:
- Automobile Manufacturing: Companies like Rajesh’s are using them for robotic assembly lines, welding, and material handling.
- Pharmaceuticals: Ensuring precise motion control in drug production and automated packaging.
- Food & Beverage Processing: Helping maintain hygiene standards with precise filling, cutting, and packaging.
- Electronics & Semiconductor Industry: Used for delicate tasks like circuit board assembly and inspection.
- Logistics & Robotics: Transforming warehouse automation with smooth, controlled movements.
The Future of Automation in India
With the Indian government’s push for Make in India and Industry 4.0, automation is no longer a luxury but a necessity. Companies investing in electric actuators today are gaining a significant advantage in cost savings, efficiency, and sustainability. Industry experts predict that within the next decade, electric actuators will become the standard across most automated processes in India.
Final Thoughts
Rajesh’s journey from frustration to success highlights the power of innovation in manufacturing. His factory’s transformation is just one of many success stories across India. As industries continue to evolve, adopting electric cylinder actuators will be a defining step towards a smarter, cleaner, and more efficient future.
For businesses looking to stay ahead in automation, now is the perfect time to explore the potential of electric actuators. The future is electric—are you ready to make the switch?