Linear actuators are an essential part of many modern devices and systems, providing the linear motion required for precise push and pull applications. These versatile components are used in a wide variety of industries, from automation and robotics to medical equipment and automotive technology. In this blog, we’ll explore the different type of Linear Actuator that are ideal for push and pull applications, helping you choose the right one for your specific needs.
Type of Linear Actuator :
1. Electric is a Type of Linear Actuator
Electric linear actuators are among the most popular types used in many push and pull applications. They convert electrical energy into linear motion, making them a clean and highly efficient option. Electric actuators are known for their precise control, easy integration, and relatively quiet operation, which makes them suitable for home automation, adjustable furniture, and industrial applications. They are commonly used in systems where precise positioning is crucial.
Advantages:
- High precision and control
- Clean, efficient operation
- Low noise levels
Applications:
- Adjustable beds and recliners
- Robotics and automation systems
- Solar panel positioning
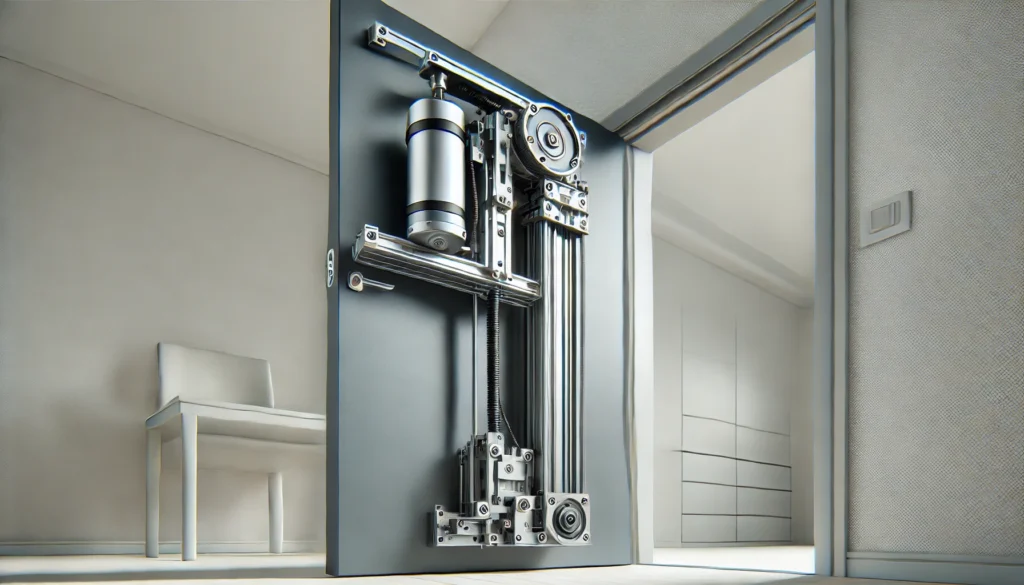
2. Hydraulic Linear Actuators (Type of Linear Actuator)
Hydraulic actuators use pressurized fluid to create linear motion, making them extremely powerful and capable of handling heavy loads. They are ideal for applications where significant force is required. Hydraulic actuators are commonly used in construction equipment, such as excavators, where large-scale push and pull actions are needed.
Advantages:
- High force output
- Reliable for heavy-duty applications
Applications:
- Construction machinery
- Industrial presses
- Aircraft landing gear
3. Pneumatic Linear Actuators
Pneumatic actuators use compressed air to produce linear movement. They are known for their rapid response times and are typically used in applications where speed is essential. Pneumatic actuators are also a cost-effective solution for systems that do not require precise control but need consistent, repetitive motion.
Advantages:
- Fast response times
- Simple and cost-effective
Applications:
- Packaging machinery
- Material handling systems
- Food and beverage production lines
4. Another Type of Linear Actuator
Stepper motor actuators combine the precision of stepper motors with linear motion, providing an ideal solution for applications where both speed and precise positioning are required. Stepper motor actuators are often used in CNC machines and 3D printers, where accurate control over movement is critical.
Advantages:
- High precision
- Good control over speed and position
Applications:
- 3D printing
- CNC machines
- Laser cutting systems
5. Ball Screw: One Type of Linear Actuator
Ball screw actuators utilize a rotating screw to produce linear movement, providing high efficiency and accuracy. They are ideal for applications that require smooth and precise push and pull operations. These actuators are often found in robotics, medical equipment, and other automated systems that require reliable performance and minimal backlash.
Advantages:
- High efficiency and accuracy
- Minimal friction and backlash
Applications:
- Medical imaging equipment
- Industrial robots
- Precision manufacturing systems
6. Lead Screw Actuators
Lead screw actuators are similar to ball screw actuators but use a threaded screw and nut to generate linear movement. They offer good precision but with more friction compared to ball screw actuators. Lead screw actuators are typically used in lower-speed applications where cost-effectiveness and simplicity are priorities.
Advantages:
- Cost-effective
- Easy to design and maintain
Applications:
- Laboratory equipment
- Adjustable seats
- Low-load positioning systems
Choosing the Right Linear Actuator
The type of Linear Actuator you choose depends on the specific requirements of your push and pull application. For heavy-duty applications, hydraulic actuators are often the best choice due to their ability to generate significant force. On the other hand, if precise control and efficiency are needed, electric or stepper motor actuators are preferable. For high-speed, repetitive tasks, pneumatic actuators are ideal due to their quick response times.
Understanding the differences between each type of actuator can help ensure that you choose the most suitable one for your project, optimizing performance, reliability, and cost-effectiveness.
Conclusion
Linear actuators play a vital role in modern automation and control systems. Whether you need precision, speed, or the ability to handle heavy loads, there’s a linear actuator designed for your specific push and pull needs. By understanding the unique capabilities of each type, you can make informed decisions that will help improve your system’s performance and efficiency.